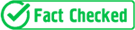
All iLive content is medically reviewed or fact checked to ensure as much factual accuracy as possible.
We have strict sourcing guidelines and only link to reputable media sites, academic research institutions and, whenever possible, medically peer reviewed studies. Note that the numbers in parentheses ([1], [2], etc.) are clickable links to these studies.
If you feel that any of our content is inaccurate, out-of-date, or otherwise questionable, please select it and press Ctrl + Enter.
A new kind of plastic can be used repeatedly
Last reviewed: 02.07.2025
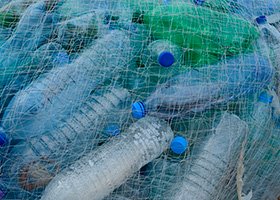
Employees of the Lawrence Berkeley National Laboratory, which belongs to the United States Department of Energy, have created a new type of polymer material. This material, like a construction set, can be disassembled and assembled, taking the necessary shape, density and color shade without losing quality. This polymer is called polydiketoenamine, or PDK for short.
Most plastic produced worldwide is not recyclable. Experts have used a new method in production that allows for molecular recycling of the product.
The well-known and most common plastic at the moment, PET (polyethylene terephthalate), is only 25% recyclable. The rest ends up in incinerators, landfills, or settles in the soil and water bodies.
Plastics are usually made up of long carbon-based molecules that are linked together to form polymers. Due to their structure, they exhibit chemical stability – that is, they do not corrode. To adapt the material to a specific use, other chemical components are added to it in production. For example, additives are needed to make the plastic softer or, conversely, denser. Subsequently, such additives can no longer be removed from the composition, even with specialized plastic processing.
Materials with different chemical components are mixed, combined and melted during the recycling process. The properties of the recycled plastic are almost impossible to predict.
Plastic recycling is a huge problem worldwide. The issue of pollution of the ecosystem is being raised everywhere, and we will most likely have to expect the situation to worsen as the amount of unrecycled and produced plastic continues to increase.
It turns out that the monomers that make up PDK are easily removed by simply immersing the material in a highly acidic liquid, which destroys the bonds between the monomers and additional components.
Scientists discovered this ability of PDK when applying various acids to glass containers used to prepare adhesive mixtures. The specialists noticed that the adhesive changed. This forced them to analyze the plastic using nuclear magnetic resonance and spectroscopy, which revealed the originality of the monomers.
Further experiments showed that the acidic environment breaks down PDK polymers into monomers, while simultaneously separating them from additional molecules. The monomers can then be re-converted into polymers, which after recycling will be completely free of other components. Experts suggest that the new type of plastic could become a promising analogue of other materials that cannot be recycled.
Experts have already planned the development of PDK plastics with a wide range of thermomechanical capabilities for subsequent use in the textile and 3D printing industries. It is also planned to manufacture new types of plastic from plant and environmentally friendly materials.
Details of the work were presented on the pages of Nature Chemistry (www.nature.com/articles/s41557-019-0249-2).